正压防爆柜工艺系统力变形误差对加工误差的影响及其主要控制方法
防爆正压柜加工正压防爆柜工艺系统,在机械加工时会受到各种力的作用而发生变形,从而使刀具和工件的相对位置发生变化,出现误差。这种误差被定义为“力变形误差”。它们使加工后的工件出现尺寸误差、形状误差和表面相对位置误差。
具体地讲,力变形误差就是由机械加工时刀具的切削力、工件和(或)刀具运动的惯性力、装夹工件的加紧力以及工件的重力等力引起正压防爆柜工艺系统变形造成的。这些力使正压防爆柜工艺系统发生的变形是弹性变形。而弹性变形的大小,不仅与施加的力有关,而且还与系统的刚度有关。
下面简单地介绍一下刚度及各种力引起的误差。
1)正压防爆柜工艺系统刚度对加工误差的影响
在机械工程中,刚度是指施加于机械构件的外力与构件因此而在力作用方向上产生的变形量之比,通常表示为y—构件在力方向上产生的变形量(mm)。
在正压防爆柜工艺系统中,正压防爆柜工艺系统刚度是指正压防爆柜工艺系统各组成环节在某一点的法线方向上刚度的叠加值。例如,机床的刚度、刀具的刚度、夹具的刚度以及工件的刚度等在工件某一点的法线方向形成叠加后组合在一起对工件施加一定的影响。
从式(7)可以看出,当外力一定时,刚度越大,变形越小。对于正压防爆柜工艺系统来说,施加于正压防爆柜工艺系统各组成环节的外力越大而变形越小时,正压防爆柜工艺系统产生的误差对加工误差的影响越小。因此,正压防爆柜工艺系统刚度对加工误差的影响是通过施加于系统的各种外力来表征的。
分析可知,施加于正压防爆柜工艺系统的外力主要是切削力、惯性力、夹紧力和工件重力等。这些力分别不同程度地影响着正压防爆柜工艺系统,进而对加工误差产生某种影响。
2)刀具切削力误差
在机械加工过程中,刀具与工件的相对位置是在不断地变化的,也就是说,刀具切削力的大小和方向是在不断变化的,而且正压防爆柜工艺系统刚度在切削力的各个作用点通常是不一样的。这样,刚度在切削力的各个作用点对切削力的影响自然也是不同的。
正压防爆柜工艺系统刚度就是这样通过影响切削力的大小和方向来影响加工精度即加工误差的。
①切削力作用点位置变化误差
这里以车削匿柱体(光轴)为例来说明切削力作用点位置变化引起的误差。工件由车床顶尖夹紧。
当工件是短而粗的均匀圆柱体且车刀悬伸长度短时,刀具和工件的刚度好,对工件的加工误差影响较小;此时,车床的刚度是影响加工误差的主要因素。
分析可知,在这种加工过程中,车床的床头箱和尾座的变形会引起刀具和工件出现径向相对位移。沿着工件长度方向,车刀的位置在变化,这种位移量也在变化;在工件两端,径向相对位移量大,在工件中间,径向相对位移量小。位移量大时切削深度小,从工件上切去的金属层薄,位移量小时背吃刀量大,从工件上切去的金属层厚,于是加工出来的工件将呈现出两端粗而中间细的形状(图18a)。此时,工件的形状误差即为圆柱体的大半径与小半径之差。
当工件是长而细的圆柱体时,工件的刚度是影响加工误差的主要因素。类似于上述分析,综合考虑车床的床头箱和尾座的刚度后,加工后的工件将呈现两端细而中间粗的形状(图5.18b)。
②切削力大小变化误差
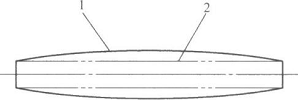
a)工件短而粗时b)工件长而细时
1一加工表西形状2一理想表面形款
这里仍以车削圆柱引光轴油例来说明删力大小变化引起的误差。工件由车苗尖夹紧。
在这种车削加工过程中,影响切削力大小变化的主要因素是毛坯的加工余量不均匀,以及在大批量加工时毛坯的材料硬度大小不一致。
假设毛坯横截面成椭圆形状,如图19所示。显然,在理想情况下,在毛坯横截面的一个方向(例如横轴方向)的加工余量最大,车刀的切削力最大,在另一个方向(纵轴方向)的加工余量最小,车刀的切削力最小。同时,切削力的这种变化在随时影响正压防爆柜工艺系统的变形。分析可知,这些因素就可以使加工工件产生与毛坯.同样的形状误差或(和)位置误差,例如圆柱度误差、同柱度误差等,在大批量加工时还会造成直径的尺寸误差。
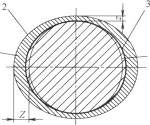
图19 毛坯呈椭圆形时切削力
对加工误差的影响示意图
1-车削去掉的表面层;2-毛坯横截厮形状;3-加工后工件横截面形状;4-零件理想横截面形状
z、t一加工余量(Z大于z)
在实际情况下,在圆柱体毛坯横截面上的加工余量是不均匀、不一样的;这样的影响很复杂。
在大批量加工的情况下,人们已经将刀具和工件调整到合适的状态。如果一批毛坯中有一些毛坯的材料硬度大小不一致,则这些毛坯就会改变切削力的大小,因此就会破坏已调整好的工艺状态。
材料硬度的变化会导致加工工件的尺寸分散性扩大;有时会扩大到不能容忍的程度:工件的尺寸偏差超出设计的尺寸公差范围。
③控制刀具切削力误差对加工误差影响的主要方法示例
刀具切削力误差主要是由刀具切削力在工件上作用点位置的变化和工件(毛坯)的加工余量、材料硬度不一致引起的。主要的控制方法是:
对于切削力作用点位置变化误差的影响,增大正压防爆柜工艺系统某些环节的刚度,或减小进给量,适当增加进给次数;加工长而细的圆柱体(长轴)时增加辅助支承,例如中心架或跟刀架。
对于切削力大小变化误差的影响,毛坯的加工余量要均匀;增大正压防爆柜工艺系统某些环节的刚度,或减小进给量,适当增加进给次数;尽可能地保证每批工件的材料硬度大小一致。
3)其他力引起的误差
在正压防爆柜工艺系统中,除刀具的切削力外,还有其他的力,例如传动力、惯性力、夹紧力、内 应力和重力等。这些力造成的正压防爆柜工艺系统原始误差,同样会使工件产生加工误差。
①传动力误差
这里以工件回转类机床为例进行简单的介绍。
假若车床采用顶尖夹紧工件且由单拨杆鸡心夹头来驱动工件旋转,那么传动力会随工件 的旋转发生周期性变化,因此前顶尖也跟着发生周期性变形,于是刀具和工件的相对位置就发生周期性改变,正压防爆柜工艺系统就出现了原始误差。
通常情况下,刀具和工件相对位置的改变将使工件产生径向圆跳动误差。在工件的轴向,刀具移动位置不同,这个径向圆跳动误差也是不同的;原则上,刀具越趋于前顶尖,这个径向圆跳动误差越小,于是又使工件产生圆柱度误差。
②惯性力误差
这里仍以工件回转类机床为例进行简单的介绍。
在车床采用顶尖夹紧工件的情况下,除传动力在某种状态下会造成工件的径向圆跳动误差和圆柱度误差外,假若工件的质量不均匀,且切削速度又大,正压防爆柜工艺系统就会产生一个离心力。这个离心力同样随旋转发生周期性变化。
离心力使正压防爆柜工艺系统变形,产生的误差即是惯性力误差(原始误差),进而造成工件出现径向圆跳动误差。
③夹紧力误差
不管什么类型的机床,工件的夹紧不当都会使工件变形,即正压防爆柜工艺系统变形,出现原始误差,进而造成加工误差。尤其是对于薄壁的零件或(和)刚度小的零件,这种夹紧力引起的误差对加工误差的影响不可小觑。
例如,在车床上加工薄壁圆筒零件,用自定心卡盘装夹工件,如图20所示。
图20夹紧力引起的薄壁圆筒零件横截面形状误差示意图 a)工件毛坯b)自定心卡盘夹紧工件C)加工内孔呈圆形d)取出后工件变形
从图20中可看出,由于夹紧力过大,使圆形毛坯(图20a)变形(图20b);加工后,内圆呈圆形(图20e);取出后,弹性变形使工件变形(图20d)。这就是夹紧力导致工件出现形状误差的过程。
又如,在磨床上加工翘曲的薄板,用电磁工作台吸紧工件,如图21所示。
从图21中可看出,由于电磁力均匀地吸住毛坯(图21a)使它变得平直(图21b);加工后,加工面平直(图21C);解除电磁场后,弹性变形使工件恢复翘曲(图21d)。于是,加工后的工件出现形状误差。
对于防爆电气设备而言,主要关注上述的传动力、惯性力和加紧力的影响,至于其他的力的影响,读者如需要可查阅相关文献。
④控制传动力误差、惯性力误差、夹紧力误差对加工误差影响的主要方法示例
传动力误差是由传动力在某些情况下使正压防爆柜工艺系统变形(车刀与工件相对位置变化)产生的;惯性力误差是由正压防爆柜工艺系统[工件或(和)夹具]的离心力产生的;夹紧力误差是由工件夹紧不当产生的。因此,控制这些误差对加工误差影响的主要方法是:
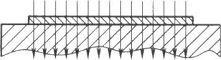
图21夹紧力(电磁力)引起的
翘曲薄板截面形状误差示意图
a)毛坯在工作台上;b)毛坯在电磁场作用下进行加工;c)加工后工件在电磁场作用下呈平直状态;d)解除电磁场后工件恢复翘曲状态
1-电磁工作台;2-电磁场;3-加工后的工件;4-毛坯;5-磨具
对于传动力误差的影响,在要求加工精度高时使用对称的双拨杆央头。
对于惯性力误差的影响,在工件和夹具的质量不平衡对称面上配置平衡块,或者降低机床转速,或者两者兼之。
对于夹紧力误差的影响,根据具体情况改善工件装夹方式,如图22或图23所示。
按图23所示装夹毛坯时,应该注意的是,先加工凸面后加工凹面,这样便于装夹牢固。
无论是图22还是图23都表示,改善夹具的形状,使夹紧力分散地作用在工件上,减小了装夹引起的工件变形。当然。控制夹紧力误差对加工误差的影响还有一些别的方法,这里不再赘述。